Mixing of Liquid Butyl Rubber
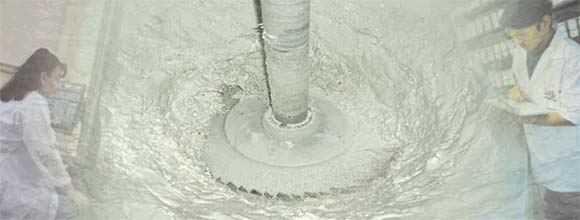
You will need an electric drill and a 3/8 inch nap roller for manual application. Mix for approximately three minutes. Chalk off your roof into 20X10 ft areas. When you are done "filling" that area you should have completely used your four-gallon pail.
Our proprietary solvent-based coating explained.
Watch our 40 second video explaining our unique drying process unlike any other coating.
Physical Makeup
Liquid Butyl Rubber is similar to traditional EPDM makeup. The most crucial qualities include:
- A high resistance to water, ozone and ultraviolet, and overall superior anti-aging characteristics
- Has a built-in mildewcide to deter mold and mildew growth.
- Our "White" is an Energy Star qualified product. A temperature tolerance that ranges from -40° to 250° Fahrenheit.
- It is both alkali and acid resistant.
- Withstands ponding water 365 days a year.
What is the Spread Rate?
The ideal thickness is 20 mil. of dry film, which can be spread to 50 square feet per gallon onto a smooth area. When assuming a 45 square foot gallon, the specs are:
- 8 pounds per mixed gallon
- 1520 psi tensile
- -62° Fahrenheit brittle point
- 180-200% elongation
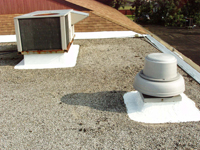
What is the Cure Rate?
The quickness of curing depends wholly on temperature and oxygen availability. Oxygen is required to activate the catalyst. Keep in mind that temperatures vary drastically in some regions, and it may take several weeks for a full cure to take place if Liquid Butyl Rubber is applied during a cooler period. We suggest applying the product during a day it is above 50 for at least three hours to waterproof. It can literally to freezing temperatures before it fully cures without hurting the product. It just won't continue to cure until it gets above 50 again during the day.
This is why the product should not be submerged under water until fully cured. However, even in a non-cured state, after 3 hours above it will withstand water and rainfall assuming proper drainage. With temperatures above 50 degrees you can expect a full cure within 8-10 hours depending on humidity. Should it fall below 50 degrees during the night you simply need to add those hours to your cure time during the day.
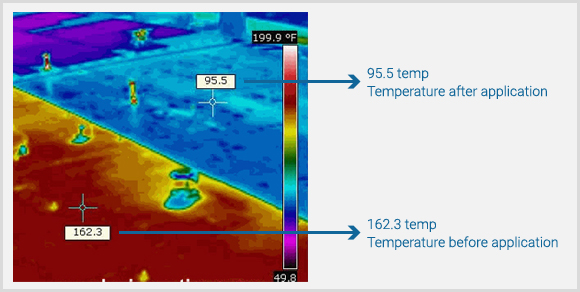
Technical Properties | ||
---|---|---|
Coverage Rate | 50 sf/gal | |
Flashpoint | 101°Fahrenheit | |
Application Temperature | Apply at temps above 50 degrees for three hours to waterproof. 8-10 hrs for full cure. Temp can fall to freezing but product will not continue to dry until temps rise above 50 again | |
Weight (lb./gal.) | 8.5 | |
Solids (% by Weight) | 50.0 1% | |
Viscosity @ 78 | 2900 cps. | |
Drying Time | 2-4 hours | |
Shelf Life | 5 Years | |
Elongation | ASTM-D-412 | 500% |
Tensile Strength | ASTM-D-412 | 1520 PSI |
Permeance (10miles) | ASTM-E-96 | 0.166 perms |
Fungi Resistance | ASTM-G-21 | 0 (Pass) |
Water Swell | ASTM-D-471 | 0% |
Weathering | ASTM-4798 | Pass |
Low Temp. Flex | ASTM-D-522 | Pass |
Wind Driven Rain | TT-C-555B | Pass |
WET ADHESION (ASTM C 794/D 903) | ||
Metal | Pass | |
SBS Mod. Bit. | Pass | |
APP Mod. Bit. | Pass | |
Smooth BUR | Pass | |
EPDM | Pass | |
TPO | Pass | |
Hypalon | Pass | |
SPUF (Foam) | Pass |
Failure to follow the directions and/or proper preparation may result in poor product parformance.
- Existing MOISTURE on/in substrate prior to coating application
- Product will take temperatures to -40 F
- Substrate insufficiently cleaned.
- Coating unable to bond to substrate.
- Improper/Inconsistent coating mil thickness.
- Leak area not identified and sealed.
- Malfunctioning spray equipment.
- Product contamination on job site.